Jewelry, Bead and PMC Kilns
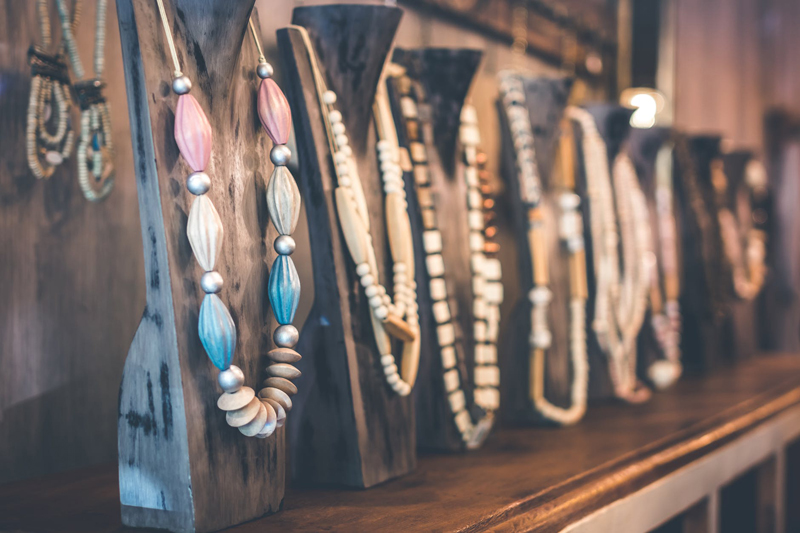
If you'd like to make larger metal clay components, glass beads and pendants, or enameled jewelry, you'll need a kiln. Kilns can be useful for some basic tasks as well, such as annealing and hardening metal wire and sheet. There are lots of kilns on the market that you can safely use at home or in a small studio. The type of kiln of you need depends on exactly what you'll be doing with it, and how much money you'd like to spend.
Here are some of the most important factors to consider when choosing a kiln.
Firing Temperature
Different tasks require different firing temperatures. The following table provides some basic temperature guidelines for popular kiln uses. (These are very general guidelines, and you should not use them for making jewelry without researching your specific task in more detail.) You'll want to make sure your kiln can reach and maintain the temperatures you need.
General Jewelry Making Kiln Firing Temperatures
Task | Temperature (F°) |
Hardening sterling silver | 600° |
Annealing (softening) sterling silver | 1110° to 1200° |
Annealing (slowly cooling) lampwork beads | Temperature needs to gradually decrease from as high as 1150° to as low as 650°. |
Firing metal clay | 1110° to 1650° for silver (1830° for gold) |
Firing enamels | 1380° to 1740°, depending on type of enamel |
Fusing glass | 1500° |
Dichroic glass | Minimum 1650° |
Glazed ceramics | over 2000° |
Temperature Regulation
Maintaining the proper temperature, or range of temperatures, during firing is essential for professional results. How you control temperature depends on how the kiln is designed.
Unregulated kilns do not have built-in temperature gauges, and they are unable to adjust their own temperatures automatically. For a kiln like this, you will need additional equipment - like a device called a pyrometer - for checking temperature on a regular basis during firing. You will also need to manually adjust the controls on the kiln to correct temperature as it rises and falls.
Programmable kilns have the ability to monitor and maintain their own temperature. You program them manually before firing, and they complete the entire firing process automatically. A programmable kiln can make complex firing tasks like lampwork-bead annealing much easier.
Be aware that some kilns may monitor their own temperature but do not regulate it. You will need to monitor and adjust temperature with these manually.
Power Source
Many kilns run on electricity, and some are powered by gas. If you choose an electric kiln, make sure it will run on the power supply you have available. Regular household plugs in North America provide 120 volts of power, rather than the 220 to 240 volts required by some more powerful kilns.
Heat-Up Time
Some kilns take longer than others to reach desired temperature. If you tend to work within tight time constraints, this may be an important factor.
Bead-Making Equipment
Glass-bead annealing requires special kiln equipment and safety considerations. The beads will be placed into the kiln while still on their metal mandrels. You'll need a kiln that can accommodate bead mandrels - and protect you from being electrocuted when you place them inside. (Frightening, but true!)
Because beads are placed in the kiln after it has reached temperture, your kiln should also have a small safety access door. This will reduce the amount of hot air that rushes out of the kiln when you open it.
Specialty kilns for bead annealing are available from the major jewelry supply houses and from many art glass suppliers.
Practical Considerations
Don't forget to consider how the size and configuration of a kiln will fit in your work area. Since jewelry doesn't take up much space, your kiln won't need to be very large. In fact, smaller kilns tend to have more even heat distribution, which produces more accurate results.
Make sure you have an appropriate area to set up and plug-in the kiln. Of course, you should locate it away from any water source and on a solid, stable surface. It's a good idea for the surface just outside of the kiln door to be heat and flame resistant, in case a hot item falls out while you're removing it.
Price
Kiln prices range from as low as around $100 to over $1,000. The least expensive models are very small and portable. Some are powered by a disposable propane tank rather than electricity. If you plan to use your kiln only once in a while, and for small projects (like simple metal clay components), a portable kiln may be a wise option. But if you'll use your kiln extensively or for larger-scale projects, consider investing in a more versatile model. For an electric 120-volt kiln for basic metal and glasswork, be prepared to pay between at least $200 to $700 for the kiln, plus around $70 to $100 for a pyrometer (if one is not included).
Of course, you should not make a purchasing decision on price alone. To avoid frustration and get the most from your equipment, make a list of your kiln wants and needs. Order them by priority, and refer to them often while you browse various models. Don't be afraid to ask questions of the seller or manufacturer if you can't find the information you're looking for.
Click here for some examples of kilns available now on eBay. You can also find them online by running a standard keyword search.
For more information on making glass beads, see Making Glass Beads, by Cindy Jenkins (available at Amazon.com).
Some links in this article point to websites not associated with BellaOnline.com. BellaOnline.com is not responsible for the material found there.
Chris Franchetti Michaels is a writer and jewelry artisan specializing in beaded designs, wire work, and metal fabrication. She is the author of the books Teach Yourself Visually: Jewelry Making and Beading, Beading Quick Tips, and Wire Jewelry Quick Tips. Visit her website BeadJewelry.net for more jewelry-making help and inspiration.
You Should Also Read:
Introduction to Metal Clay Jewelry Making

Related Articles
Editor's Picks Articles
Top Ten Articles
Previous Features
Site Map
Content copyright © 2023 by Chris Franchetti Michaels. All rights reserved.
This content was written by Chris Franchetti Michaels. If you wish to use this content in any manner, you need written permission. Contact Susan Mendenhall for details.